Is FSC/SFI certification a sham? Is there really FSC-certified pulp in the FSC-certified paper you buy? What about recycled pulp? Can you trust anyone?
PaperSpecs recently published a great post to clarify chain of custody certification - what it is and what it isn't.
Here's what
Sabine Lenz, founder of PaperSpecs, had to say:
“This is a sham,” Cynthia was up in arms, “A friend told me that there actually might not be any FSC-certified pulp in the FSC-certified paper that I buy! Then what about recycled pulp and … what is all this talk about auditing and … how can I trust anybody anymore?”

Okay, I never said eco-certification was easy, but Cynthia’s friend definitely didn’t do the best job at explaining the ins and outs. So let me try.
FSC, and SFI for that matter, both certify forests to ensure they are managed in an environmentally and socially responsible manner. Yes, they have differing standards, but I’ll write about this aspect in the coming weeks.
For now, let’s just keep it simple and say this: Both FSC and SFI care deeply about our forests and the environment. Their respective labels provide you and me with the assurance that the paper products we’re purchasing come from forests managed to conserve biodiversity and support local communities.
This is what we all have heard for years now. It is a good and noble cause, and we support it.
Where does the pulp come from?
As we agree on this, we can also agree on the fact that the FSC/SFI pulp has to come from certified forests. The certification of the forest as such is the part you and I can easily understand.
An independent auditor (both SFI and FSC work with third-party auditing companies) goes out to the forest that wants to be certified and makes sure it fulfills all the criteria required by the certification model.
This doesn’t just include visiting the actual forest, but also includes aspects like: making sure the forest workers are skilled; ensuring that no pesticides are used in managing the forest or that no genetically modified trees are planted – the standards are extensive.
Once the trees are ripe (fully grown), they are harvested and brought to a certified pulp mill.
NOTE: There are only around 40 FSC-certified pulp mills in North America producing somewhere between one and three million tons of certified pulp. Some of these mills produce their own paper from this pulp, but many paper mills in North America are non-integrated (meaning they don’t make their own pulp). Non-integrated mills buy their FSC-certified pulp from those certified pulp mills on a contractual or first-come, first-serve basis.
How is the pulp handled?
If we all wanted to buy 100 percent certified papers tomorrow, there just would not be enough pulp available to keep up with the demand. So, the most common logos we see today are those of “mixed sources,” papers that contain a certain percentage of certified pulp. Are you still with me?
The original idea – and a logical one at that – was to ask the mills to ensure that the certified pulp was stored separately from the rest of the mill’s pulp and was used in the papermaking process separately and … But if you have ever been at a paper mill, this poses quite a challenge.
For one, a paper machines run 24/7 (except the yearly downtime for maintenance), so asking a mill to stop and start the machine to make certified paper is an economic impediment.
Volume Sharing
Over the years, in an attempt to make the production of certified papers economically viable, FSC and SFI have adopted a “volume credit” system. A confusing term to be sure. I prefer “average percentage.” Let me explain with an example.
A mill produces 100 tons of paper a year. It buys 10 percent of the pulp needed from a certified pulp mill. In order to not have to interrupt its workflow, the mill and certifying body agree that this 10 percent can be called out on specific paper lines the mill produces. In our case, theoretically 100 percent of the mill’s paper could be called out as 10 percent FSC /SFI certified.
So far this all makes sense right?
Let’s take it one step further and say the mill wants to offer a specific paper line with a higher certified percentage to its customers – Brand XYZ is 20 percent certified. Now the mill can only label 50 percent of the papers it produces as 20 percent certified.
The Audit
The certifying body keeps a close eye on its mill clients and conducts yearly audits, which include lots of paperwork including checking invoices for certified pulp received to ensure that a mill doesn’t market or claim to have more certified papers than the percentage of certified pulp that it purchased allows it to claim.
This again is to assure you and me that we get what we pay for.
Does this mean that theoretically the specific paper you and I buy does not contain the full 30 percent FSC / SFI pulp it claims? Sorry, but yes.
And by the way, the same “average percentage” principle applies to the recycled content claims made by pulp and/or paper manufacturers.
The bottom line is that we are “paying” for the overall efforts a mill makes to be sustainable and offer certified papers, thus providing our forest managers the incentive to certify, while staying economically viable.
About PaperSpecs
Finding the most accurate information on paper availability, green certifications and trends like digital paper options is a challenge for designers, print buyers and paper purchasers worldwide.
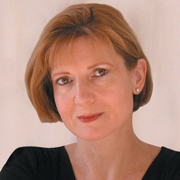
This reality inspired Sabine Lenz, designer and author, to create PaperSpecs, the first independent and comprehensive Web-based paper selection tool. The search mechanism is specifically designed to help paper specifiers easily and quickly find the paper that meets their project’s sustainability goals, creative vision and process requirements.
PaperSpecs currently features more than 4,300 papers from over 70 mills with a staff dedicated to updating the specifications daily. PaperSpecs members have access to this powerful database as well as the ability to order sample sheets and the latest swatchbooks and mill promotions.
Take a
virtual tour of this convenient, current and comprehensive online paper selection tool to see how you can find the perfect paper in less than 60 seconds.