"Going green" is a term that has been on every printer's lips for the last year. Regardless of which side you fall on - going green or waiting to see - your customers are thinking green.
Compare the results of two surveys that were completed not many months apart.
Forrester Research published survey results in Q4 2007 which showed that consumers who responded indicated that 63% were concerned about the environment and 50% were more concerned about the environment than they had been a year before. Survey results came from the
Retail, Marketing, Customer Experience, And Service Benchmark by North American Technographics. (PDF, 1MB)
While print service providers generally sell to businesses, the people in those businesses are the consumers surveyed by Forrester. Every one of them goes home from work and makes statements like these:
- I am concerned about the amount of gas my car uses. (67%)
- I regularly recycle paper, bottles, and cans. (66%)
- I am concerned about the environment. (63%)
- When purchasing products, I look for energy-efficient labels; e.g., ENERGY STAR. (49%).
And when they come back to work, those same attitudes can influence their business purchases. In
Printing Goes Green, a report available from the
WhatTheyThink store, Richard Romano described the results of a survey of print service providers completed in Q1 2008. Printers have a slightly different perspective of their customers' green views. For example, when asked how important "sustainable printing" is to their customers, respondents having 20 to 49 employees said:
- It is critically important to most of our customers. (1.3%)
- It is critically important to only a select few customers. (52.0%)
- It is not essential to our business or to our customers. (36.0%)
Even though there seems to be a disconnect between consumers' views and printers' perceptions, printers are implementing initiatives that make their processes or products more efficient and environmentally sensitive. Those same small printers, having 20 to 49 employees, said that they:
- Promote recycled papers as better than "typical" papers. (22.7%)
- Identify their company in marketing and sales materials and promotions as an environmentally sensitive business. (36.0%)
- Justify new equipment purchases because of their more favorable environmental impact. (26.7%)
- Have special "green" certifications from independent organizations. (30.7%)
- Perform an "environmental impact" statement or audit. (14.7%)
A visit to two printers in the Vancouver BC metro area, gave us an opportunity to see what small printers are doing to change their operations to be more environmentally aware.
Marine Printers, Vancouver BC
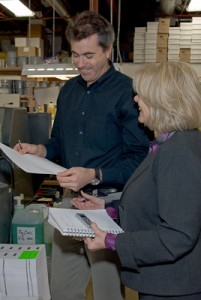
Founded in 1931,
Marine Printers is now run by
Matt McKenzie and
Bill George, the third generation of printers in the family. Located deep in the heart of Vancouver - where staff have access to excellent public transportation - Marine Printer blends tradition and technology.
In his office, Matt treasures an antique wooden cabinet containing wood and lead type used by the first two generations of McKenzies.
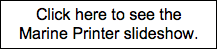
Just around the corner from his office is the prepress operation and a Creo computer-to-plate system, installed four years ago.
"Green printing" is not limited to FSC-certified paper and vegetable-based inks. New technology reduces the waste generated throughout the production cycle.
"The CTP is quicker and more efficient," said McKenzie. "We use a gum/rinse process, and there are no chemicals involved. We're hoping to get the process-less plates soon, at the same time we're looking at the water-wash plates."
The lean manufacturing experts tell us that "waste" can also be measured in time. By integrating the CTP system - which eliminates film and chemical processing - with a new Komori Lilthrone press, ink profiles presetting and automated press make-ready cut back not only on press setup time, but on the number of sheets required to bring the press up to color. And the pressmen reuse the "overs" for the next make-ready, before putting them in the recycle bin.
Also on the floor is a 4-color Heidelberg GTO press, a perfecting press that prints both sides simultaneously. Aqueous coatings are applied and dried inline, allowing the pressman to move the printed sheets to binding and finishing immediately.
Using the right-sized equipment for the job can also be "green." Rather than let his GTO go, Bill George - Matt's brother in law and business partner - uses the 10-year old press to compete with digital printing on short runs. Overprinting on as few as 50 sheets can be very cost effective.
Marine Printers delivers on the green mandate to reduce, reuse, recycle, and replace. In this case, small is not only beautiful, small is green.
3S Printers, Richmond BC
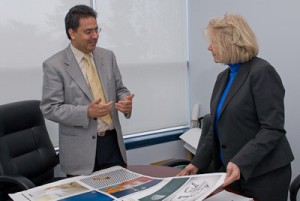
Fast forward from 1931 to 1991, and witness the birth and development of
3S Printers; a company that decided to not only reduce, reuse, and recycle but to replace old equipment with the latest technology.

Growth by acquisition made it necessary for
Dave Sandhu to move his company into a new facility in 2006 that had been specially built to incorporate state of the art technology. The HVAC system is computer-controlled to optimize energy use. By combining natural light in the offices with parabolic fluorescent lighting, 3S has reduced the number of bulbs needed for proper lighting.
"We rolled four companies into one, got rid of the old equipment and brought in new, more efficient equipment based on new technology," said Dave Sandhu. "We chose to go to UV technology because it is both green and delivers a high-quality, bright, sharp print on uncoated and recycled papers."
The move encouraged Sandhu to get rid of all the old equipment that came with the acquisitions and replace it with new, more efficient technology like the KBA Rapida. By applying UV technology and special coatings, the Rapida allows 3S to offer extremely sharp vivid images and text on any substrate.
Printing with UV inks means that 3S can offer their customers a green solution that:
- Gives a bright, sharp print on uncoated and recycled papers because the inks sit on top of the paper and are not absorbed.
- Incorporates special coatings and varnishes developed for the packaging industry
- Avoids the release of VOCs into the air
- Prevents scuffing during finishing because the inks dry immediately.
Implementing JDF throughout the entire production process - estimating, production planning, prepress, printing, and finishing - is the next step in lean manufacturing. 3S is in the process of implementing the HiFLEX management information system and all the information needed to mange production will follow the job from prepress through finishing, and "intelligent" equipment reduces make ready time and waste.
While newer, faster, smarter equipment makes for a more efficient process for long runs, 3S - like Marine Printer - also has "right-sized" equipment on the floor. An old Heidelberg still does its duty for die cutting and embossing.
Efficient production processes are critical, however even the most efficient processes have some waste. Dave and his staff are separating all paper, cardboard, metal, and plastics into bins, drums, and barrels for recycling. Inks are remixed and reused as much as possible, and 3S even has a "can press" that compresses ink cans to reduce the space needed for storage until they are recycled.
What You Can Do
Regardless of your operation, as you look to "go green" you can also incorporate initiatives like these:
- Maintain your HVAC system; have ducts checked for leaks annually and make sure your heating and air conditioning units are working at maximum efficiency.
- Consider production at night - either longer days or night shifts - when there is less demand for electricity and rates may be cheaper.
- Design and construct new facilities to maximize active and passive solar energy.
- Insulate your shop to cut down on heating and cooling requirements by installing high r-value insulation.
- Measure and mix inks for each project. Re-mix and re-formulate waste ink for other projects or recycle it.
- Recycle all paper waste including trimmings and production waste and office paper products.
- Recycle all wood pallets and crating.
- Recycle all plastic containers and packaging shrink-wrap.
- Recycle metal printing plates, steel pallet strapping, and other metal materials. Return metal drums to the supplier to be refilled.