Contributed by Gary Conner
I've yet to meet a baby boomer who hasn't seen
Monty Python's movie where the inhabitants of a castle catapult a cow toward an invading military force.
While the image is familiar, most people do not know that it is based on a real event that happened in the 14th Century.
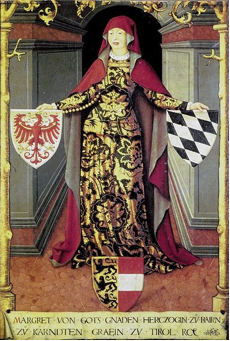
In 1334,
Margartea Maultasch of Tyrol and her army encircled the castle of
Hochosterwitz in Carinthia. Because of the steep terrain, a traditional storming of the castle was out of the question. They decided to starve out the inhabitants.
The situation inside the castle was desperate, supplies were scarce and they were soon down to their last two bags of corn, and one skinny cow.
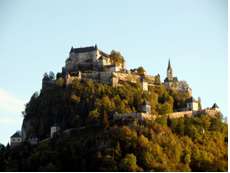
The commander of the castle took desperate action, he slaughtered the cow and filled it with the corn, ordering his troops to catapult the dead cow over the wall toward the enemy.
The invading hordes interpreted this as a clear message that starving them out was useless; obviously they had food to waste. The invaders picked up and moved on.
What does this have to do with lean manufacturing?
For the last few months we have seen over 100,000 jobs lost in the automotive industry alone. Our economy is on the brink of implosion, evidenced by an urgent effort to shore up a once powerful system.
Unless we apply significant and radical approaches to the way we run manufacturing businesses we will see ourselves "starved out."
The systems that worked for our dads and granddads are no longer viable. There is a risk that we have been lulled to sleep by the relative insulation of unique capabilities that our parents and grandparents had.
After World War II the manufacturing capabilities of the rest of the world had been dismantled, destroyed or modified to support the war efforts. Our parents and grandparents had the market cornered. Customers were beating down their doors to get product manufactured.
That condition has changed dramatically.
Now it is a "ME TOO" marketplace. In the current environment, we compete with countries that have not only rebuilt their manufacturing capabilities, but have done so using techniques like "Lean Manufacturing," based on the Toyota Production System. Our competitors may have the additional advantage of paying significantly lower wages, providing little or no benefits, and they may ignore the long term cost of unsafe working conditions or environmental concerns.
All of which contributes to an unfair and unlevel playing field.
In order to compete responsibly we cannot lower our standards regarding worker safety, diminish our concern for the environment, or hope to retain skilled team members without rewarding them financially.
But we do have to do something.
As Monty Python would say: "Something completely different!"
We have to end the "We/Them" management-by-the-old-rules methodology. We have to eliminate the old school "economic order quantity" - bigger is better mentality - that has poisoned our logic over the past one hundred years.
We have had thirty years to learn from
Toyota,
John Deere,
Pella Windows and other world class companies, to adopt and adapt our
Sales,
Order Entry,
Purchasing,
Scheduling,
Manufacturing and
Delivery systems. However, the majority of the companies I visit stubbornly refuse to acknowledge that there is a better way. They take the stance that: "If it were good enough for Dad and Granddad, then it's good enough for me!"
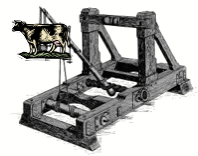
We have to be willing to catapult the cow, try something completely unexpected in order to get the result we want. I am not recommending that you throw the entire company over the wall. Begin with a model line. Take 20-25% of your company, a significant percentage, and begin applying the lean manufacturing principles. Start small, but start!
My message, my warning to all manufacturers is this: If we wait six months we will be six months further behind.
There are many companies who have decided not to wait for someone else to bail them out. They are taking decisive action. Some regions are putting together "high performance consortia" to pool resources, share knowledge, build networks and seek the common good for all the manufacturers in their region.
The recent effort by the government to bail out the failing economy is like handing out money to compulsive gamblers as they enter casinos in Las Vegas.
Dr. Phil said it best: "You cannot solve money problems with money!" When an individual is prone to overspend and squander their resources, giving them money only enables the bad behavior. They have to be retrained, reprogrammed to think ahead, plan and see the cause and effect of their actions.
In manufacturing we have been taught for decades that we must build large quantities using shared resources, huge machines, and costly tracking systems in order to cover the cost of enormous set-up times on complicated equipment. World class companies are showing us that there is a different path: smaller lot sizes, right-sized equipment, smaller value stream structure, visual signals, quick set-ups and high velocity that require little or no tracking.
Lean manufacturing is not rocket science. Lean manufacturing is a systematic and repeatable process to identify and eliminate waste. Lean manufacturing is no longer an option.
And it doesn't apply just to manufacturing. The entire enterprise must adopt these principles. And soon!
Gary Conner
Lean Enterprise Training
Editor's Note: You may read about Gary's methods in his book
Lean Manufacturing for the Small Shop. In upcoming guest posts and in links to white papers and reports, we will be publishing content from Gary Conner and other
Lean Manufacturing consultants; watch this space!
GNK